Jooteribade üle arutledes peame kõigepealt täpselt määratlema SMT defekti. Plekist rant asub ümbervoolaval keevitatud plaadil ja näete kohe, et see on suur tinakuul, mis on paigutatud vookogusse, mis paikneb väga madala maapinna kõrgusega diskreetsete komponentide kõrval, nagu lehttakistid ja kondensaatorid, õhukesed väikesed profiilpaketid (TSOP), väikese profiiliga transistorid (SOT), D-PAK transistorid ja takistussõlmed. Tinahelmeid nende positsiooni tõttu nende komponentide suhtes nimetatakse sageli "satelliitideks".
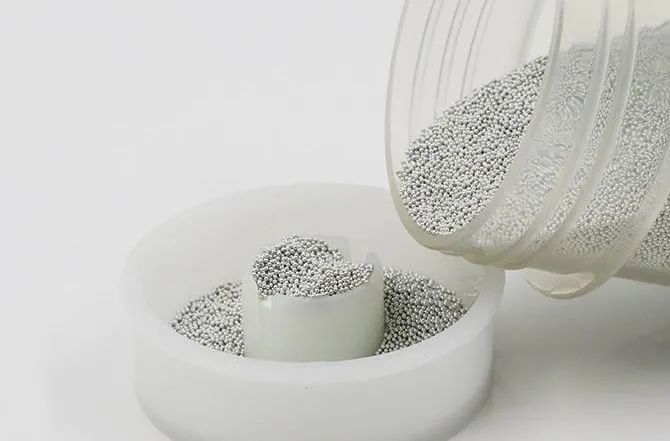
Plekist helmed ei mõjuta mitte ainult toote välimust, vaid veelgi olulisem on see, et trükiplaadil olevate komponentide tiheduse tõttu tekib kasutamise ajal liini lühise oht, mis mõjutab elektroonikatoodete kvaliteeti. Plekist helmeste tootmisel on palju põhjuseid, mis on sageli põhjustatud ühest või mitmest tegurist, seega peame ennetus- ja täiustamistööd tegema, et seda paremini kontrollida. Järgmises artiklis käsitletakse tegureid, mis mõjutavad tinahelmeste tootmist, ja vastumeetmeid tinahelmeste tootmise vähendamiseks.
Miks tekivad tinahelmed?
Lihtsamalt öeldes seostatakse tinahelmeid tavaliselt liigse jootepasta ladestumisega, kuna sellel puudub "keha" ja see pigistatakse diskreetsete komponentide alla, et moodustada tinahelmeid ning nende välimuse suurenemine võib olla tingitud loputusvedeliku kasutamise suurenemisest. - jootepastas. Kui killu element on paigaldatud loputatavasse jootepastasse, pigistab jootepasta suurema tõenäosusega komponendi alla. Kui ladestunud jootepastat on liiga palju, on seda lihtne välja pressida.
Peamised tinahelmeste tootmist mõjutavad tegurid on järgmised:
(1) Malli avamine ja plaadi graafiline disain
(2) Šablooni puhastamine
(3) Masina kordustäpsus
(4) Tagasivooluahju temperatuurikõver
(5) Plaastri rõhk
(6) jootepasta kogus väljaspool panni
(7) Tina maandumiskõrgus
(8) Lenduvate ainete gaasi eraldumine liiniplaadis ja jootekindluskihis
(9) Seotud vooluga
Plekkhelmeste tootmise takistamise viisid:
(1) Valige sobiv padigraafika ja suuruse kujundus. Tegeliku padjakujunduse korral tuleks see kombineerida arvutiga ja seejärel vastavalt komponendi pakendi tegelikule suurusele, keevitusotsa suurusele, et kujundada vastav padja suurus.
(2) Pöörake tähelepanu terasvõrgu tootmisele. Jootepasta prinditava koguse kontrollimiseks on vaja reguleerida ava suurust vastavalt PCBA plaadi konkreetsele komponendi paigutusele.
(3) Soovitatav on, et PCB-plaadid, millel on BGA, QFN ja plaadil tihedad jalakomponendid, võtaksid kasutusele ranged küpsetusmeetmed. Jooteplaadi pinna niiskuse eemaldamise tagamiseks, et maksimeerida keevitatavust.
(4) Parandage malli puhastamise kvaliteeti. Kui puhastus pole puhas. Jootepasta jääk malli ava põhjas koguneb malli ava lähedale ja moodustab liiga palju jootepastat, põhjustades tinahelmeid
(5) Seadme korratavuse tagamiseks. Kui jootepasta on trükitud, siis kui nihe on malli ja padja vahelise nihke tõttu liiga suur, imbub jootepasta padjast väljapoole ja pärast kuumutamist tekivad plekkhelmed kergesti.
(6) Kontrollige paigaldusmasina paigaldusrõhku. Olenemata sellest, kas rõhu reguleerimise režiim või komponendi paksuse juhtseade on ühendatud, tuleb sätteid tinahelmeste vältimiseks kohandada.
(7) Optimeerige temperatuurikõverat. Reguleerige tagasivoolu keevitamise temperatuuri, et lahusti saaks paremini platvormil lenduda.
Ärge vaadake "satelliit" on väike, üks ei saa tõmmata, tõmmake kogu keha. Elektroonika puhul on kurat sageli detailides. Seetõttu peaksid vastavad osakonnad lisaks protsessitootmispersonali tähelepanule tegema ka aktiivset koostööd ning suhtlema protsessipersonaliga õigeaegselt materjalide muudatuste, asenduste ja muude küsimuste osas, et vältida materjalide muutustest tingitud protsessiparameetrite muutumist. PCB vooluringide projekteerimise eest vastutav projekteerija peaks suhtlema ka protsessipersonaliga, viitama protsessipersonali probleemidele või ettepanekutele ja neid nii palju kui võimalik täiustama.
Postitusaeg: jaan-09-2024